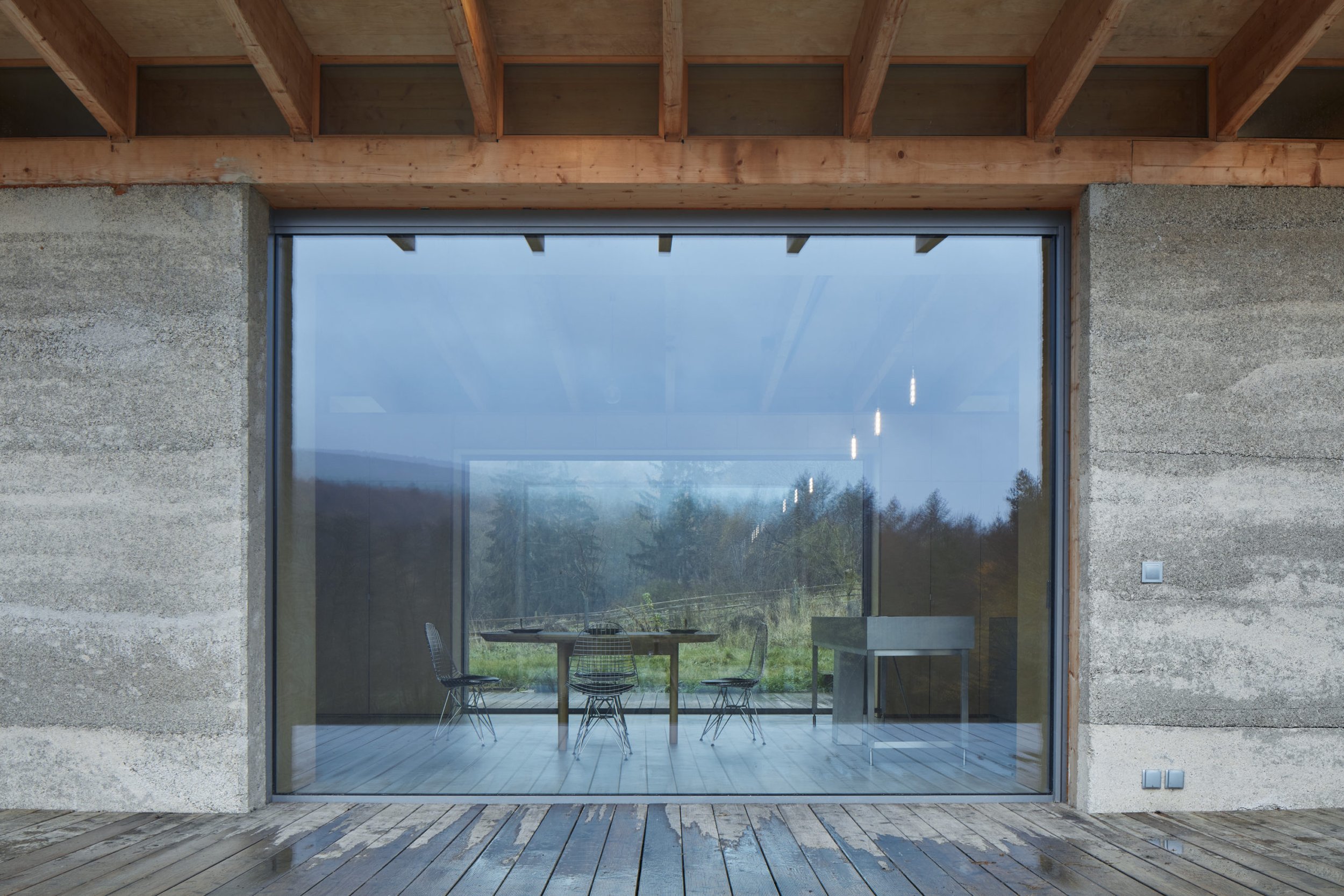
Hempcrete
Decarbonising Construction
After water, concrete is the most widely used substance on the planet. If the cement industry were a country, it would be the third largest carbon dioxide emitter in the world. Cement production alone generates around 2.5 billion tonnes of CO2 per year—about 8% of the global total.

The time it takes you to read this sentence, the global building industry will have poured more than 19,000 bathtubs of concrete.
About Hempcrete
Hemp has high silica content, a unique quality among natural fibre plants, which means it binds well with lime into a high insulating cementitious material that can be pre-fabricated into blocks or cast on site. Hempcrete is a biocomposite made from the stalk of the hemp plant (aggregate) and a mixture of calcium hydroxide and pozzolana (binder).
CO2 is absorbed from the atmosphere by hemp as it grows. During the curing process, as lime turns to limestone, the carbonation of the lime, adds to this impact, and as a result gives it a carbon negative footprint when used in buildings. Compared to concrete, hempcrete blocks are considerably lighter, which can massively reduce the energy used to transport the blocks.
It acts as an insulator and moisture regulator while lacking the brittleness of concrete, meaning that no expansion joints are required. The structure of the hemp blocks makes them excellent acoustic insulators: they dampen and absorb noise and are highly suited to areas at risk of seismic activity, as it is a low density material and resistant to cracking under movement.
It is able to naturally regulate a building's humidity and temperature, which can reduce condensation and energy consumption and improve thermal comfort for occupants. It provides natural insulation that is airtight, breathable and flexible. It is also toxin free, impervious to mould and pests, and highly fire resistant.

Stonham

Dorset

Felbrigg

Colonsay
FAQs
-
The most extensively tested and used product is hempcrete in walls. It can also be used for the ceilings and floors of buildings. Hempcrete must be used with a structural element i.e. a timber frame which has a lower carbon footprint to steel which may also be deployed.
Spraying or moulding on site is the preferred method at present, but for industrial scale uses a precast block or panel may be more suitable.
The oldest hempcrete buildings in the UK are around 23 years old, and these buildings may last for hundreds, if not thousands of years.
-
No, today it isn’t a direct replacement, but can be used as an alternative where there is structural support such as steel or glulam.
The non-load bearing nature of the material means there are instances where it may not be suitable but the significant thermal and carbon impact provide a viable way to move the concrete industry into a more sustainable path.
We are undertaking research to widen the use case of hempcrete.
-
Through its growth cycle hemp sequesters CO2, resulting in a carbon negative outcome. Once formed into hempcrete, further CO2 is absorbed as the material fossilises and is permanently bonded into the material for the full lifetime of the product.
Hemp can also be grown and used locally, improving biodiversity where it is cultivated. Due to its rapid growth cycle it is also a weed suppressant.
-
The materials have varying levels of UK (BS), European (EN), US (ASTM) and Australian (BCA) building standard compliance, with Europe and the UK leading Australia and the US in testing and length of time in use.